Smart Operating
GC has adopted innovative technologies to design, develop and improve its production processes in order to align it with the principles of circular economy. By maximizing resource efficiency, utilizing renewable energy to mitigate the impacts of climate change, and stabilizing the production processes in the past year, GC has developed of business operation in accordance with ‘smart operating’, as well as GC is enhancing collaboration on sustainability through the participation of all sectors. Over the past years, GC has implemented projects aligned with Smart Operating, as follows.
Examples of the Energy Conservation Projects
The project to improve the efficiency of distillation columns by adjusting the Reflux Ratio to the point of maximum efficiency has resulted in reduced energy consumption while maintaining or improving the quantity and quality of the gas products.
Reduction of Energy Consumption
GJ per year
Reduction of GHG Emissions
tons CO2 equivalent per year
Reduction of Costs
million baht per year
Gas Turbine Generator and the Heat Recovery Steam Generator project to enhance the overall efficiency in electricity generation of Utilites Plant and lower fuel consumption in production.
Reduction of Energy Consumption
GJ per year
Reduction of GHG Emissions
tons CO2 equivalent per year
Reduction of Costs
million baht per year
Energy Conservation Programs
Read moreAlternative Energy Project
GC has installed solar rooftop systems on the rooftops of five of its factories and has also developed solar floating systems. GC also has developed an energy storage system (ESS) to work in conjunction with solar power generation, producing electricity for internal use. These systems can generate 10,148 megawatt-hours of energy.
Generate a maximum electricity of
MWh
Reduce greenhouse gas emissions by
tons CO2 equivalent per year
Reduced energy purchased cost
million baht per year
Renewable Energy Programs
Read morePollution and Waste Reduction Projects
GC has committed to managing waste efficiently and for maximum benefit, aiming to minimize waste generation and reuse materials both in the production process and office spaces. The company has implemented the strategy of fostering an environmental culture through the 5Rs (Reduce, Reuse, Recycle, Refuse, Renewable) for environmental management, balancing resource management with sustainable business operations through the principle of Operational Eco-efficiency. In 2023, the company carried out several waste management projects, such as the project to reuse thermal insulation.
Reuse Insulation
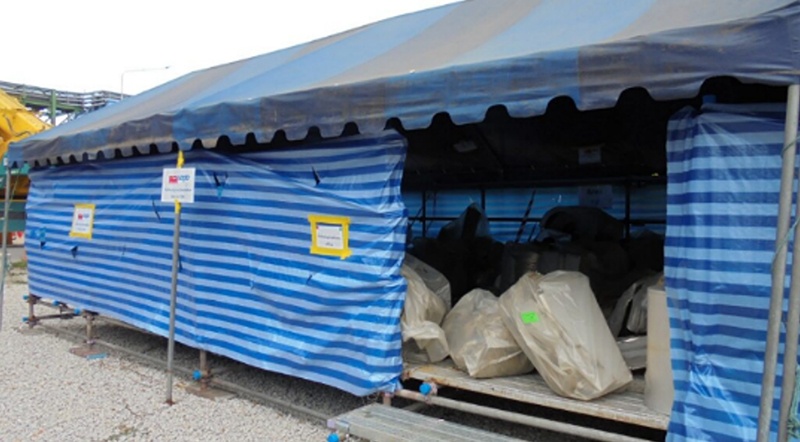
GC has continuously extended its Green Turnaround project, focusing on the efficient use of resources and reducing both hazardous and non-hazardous waste generated from maintenance activities. The project applies circular economy concepts by minimizing waste at its source and repurposing the waste for beneficial use, thus reducing the burden of waste disposal. Examples of activities include maintaining the quality of thermal insulation for reuse by implementing careful management practices, such as minimizing damage during insulation removal, storing insulation in appropriate containers, and preparing proper storage areas to keep it in good condition and dry.
Average insulation recycling more than
* Note: Figure from 2023 performance
Reusing Waste as Alternative Raw Material
- Using Mercury waste from the Aromatics and Refinery plants as raw material for medical equipment production.
- Promoting and encouraging employees to segregate waste in office, e.g. segregating plastic, glass, and paper waste for recycling and segregating food waste to be used as animal feed by the surrounding community, etc.
- Installing Seawater Reverse Osmosis (SWRO) and Wastewater Reverse Osmosis (WWRO) systems to monitor and improve wastewater quality discharged from wastewater treatment system to ensure that the discharged amount can be used and reentered in the operating process.
- Reusing off gas from Aromatics Plants, i.e. ethane, propane, butane, as substrate for olefins plants instead of flaring for over 157,000 tons per year.
- To utilize Fine polymer as recycle raw materials in manufacturing. This results in reduce consumption of Styrene monomer as a raw material in manufacturing process and increase yield for more than 96%.
- Increase Tail Gas value as raw material for Crackling Heaters and Oleflex Heaters at the Olefins Plant, which can reduce a flare loss of up to 648,000 Nm3
- Enhance the value of by-products from the OLE4 operation area by using Export Raw Pygas (Pyrolysis Gasoline) as a feedstock for the aromatics plant. Additionally, by-products in the form of C9A are sent as feedstock and products to oil refineries, resulting in increased value for the company's by-products.
Waste Management
Read moreReduction of Dependence on Limited Resources
We employ innovation to manage our water supply in the system by reutilizing water and ultimately eliminating wastewater discharge.