Process Safety Management
Process Safety Management GRI 403-2 (2018), 403-4 (2018), 403-7 (2018)
GC uses Process Safety Management as a part of our GC Management System (GCMS). The system covers all processes from design to operations, using a Hazard and Operability Study (HAZOP) as well as a Bow Tie Validation process to conduct risk assessments. The objective is to ensure a proper plan for risk management, prevention, and control in production processes, both for normal operations and emergencies, while carrying our constant reviews and updates on the emergency plan, maintaining performance standards and developing efficient and safe production processes.
GC Management System (GCMS)
Process Risk Management, Prevention and Control GRI 403-2 (2018)
GC has adopted the Hazard and Operability Study (HAZOP) to assess risks in the production process and prioritize them. This technique contemplates hazards that could potentially occur in the production process to seek risk prevention methods and control possible disruptions in the operating system. It also establishes plans to mitigate any severe impacts from potential incidents. Process risks are assessed to authenticate the efficiency of current safety systems, and install additional equipment or occur effect changes to the production process. The entire procedure has been assigned under the responsibility and governance of the Technical Safety and PSM Team to ensure efficiency throughout the production process.
GC HAZOP Study Process
According to the occupational health and safety risk and hazard evaluation in 2024 key risks detected include 1) Safety Risk (Process Safety Event): leakage of hazardous chemicals posing risks to operational safety and serious accidents resulting in injuries or fatalities, and 2) Safety Risk (Personal): risk of accidents from factory operation activities, turnaround activities, construction projects and other supporting activities that may lead to accidents and work-related injuries or fatalities.
Furthermore, Operational Area Core Team (OACT) and Process Safety Management Taskforce (PSMT) have been appointed for each production unit to drive Process Safety Management and support each working area. This contributes to GC’s target of becoming the leader that can maintain international standard in OHS within chemical industry.
Moreover, GC has conducted measures for managing reliability and integrity of machineries at all factories and established Reliability Improvement Team (RIT). Machineries at all factories will be assessed through the Asset Integrity Assessment by an internal specialist, to analyze and set an improvement plan for reliability and integrity. The improvement plan covers all factors, which are potential causes of accidents as well as reducing the number of unplanned shutdowns.
Process Safety Projects GRI 403-2 (2018), 403-4 (2018)
GC continuously raises safety standards in production processes by applying technology in operations while comprehensively developing and upgrading numerous successful pilot projects. GC has conducted numerous process safety projects, such as Enhancing Plant PSM Committee Performance, Operation Risk Management Risk Treatment to Prevent LOPC, and Align Field Risk Assessment (FRA) Good Practices.
in order to ensure the company’s production processes are safe and comply with the laws and internationally-recognized standards.
Smart Process Safety Event (PSE) Project
GC has developed a digital system to support maximum efficiency and effectiveness in Integrity Operating Window (IOW) management. This digital system tracks the Process Safety Near Miss (PSE Tier3b), from which data is used to monitor and predict accident probabilities and establish appropriate risk mitigation measures. This contributes to the prevention of equipment damage or production process disruption. Furthermore, the system can be adapted to evaluate the equipment age and plan for inspections
Align Field Risk Assessment (FRA) Good Practices
GC has collaborated with DuPont on conducting an FRA (Field Risk Assessment) and organizing training for employees to understand and identify the risks from any deviation from standards of production activity. The FRA is expected to increase the effectiveness of Barrier of Protection and reduce risk in process safety particularly in 3 dimension: Personnel, Facilities and Technology.
In 2024, GC enhanced the implementation of Field Risk Assessment (FRA) by aligning good practices and developing competencies for employees at the operating level and enabling their risk sensing skills in the workplace or work process. This was achieved through the use of the Field Risk Assessment Library (FRA Library), a database designed to strengthen proactive risk prevention in the workplace. In 2024, 76% of employees at the operating level were capable of identifying risks and inspecting FRA Sub-elements.
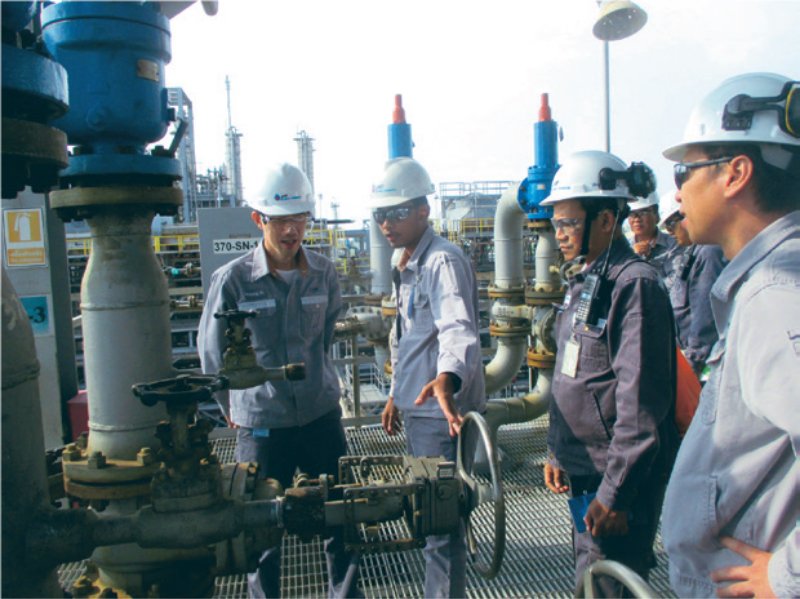
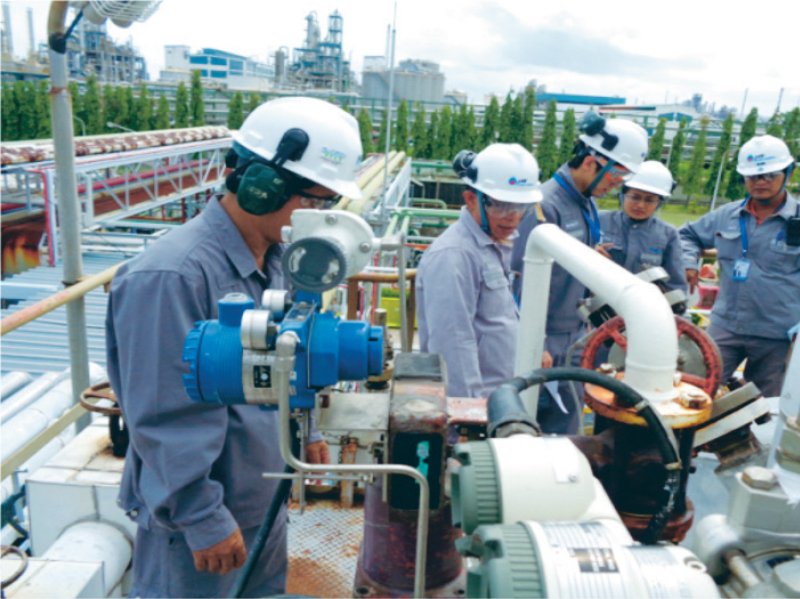
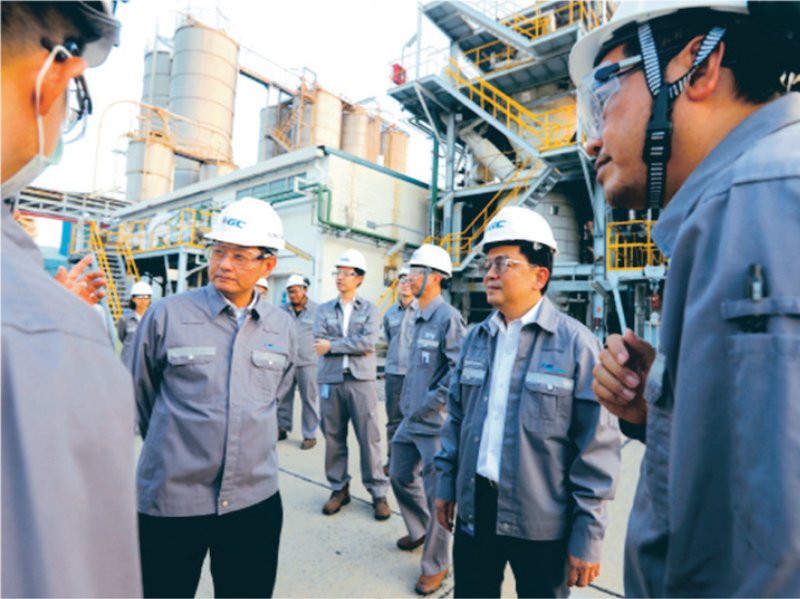
Strengthening Bow Tie Barrier Validation
GC has applied Bow Tie risk analysis to assess potential hazards or accidents as well as any impact that may lead to Major Accident Event (MAE). The company has improved the assessment of operational effectiveness in each bow tie by examining the data for accuracy and integrity, incorporating them into the annual process safety management’s internal audit process as the regulations of the Industrial Estate Authority of Thailand (IEAT) in order to ensure that the established measures are ready to prevent process safety incidents.
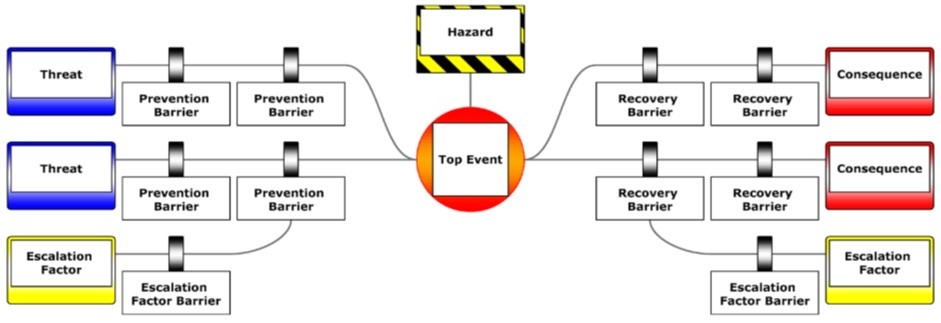
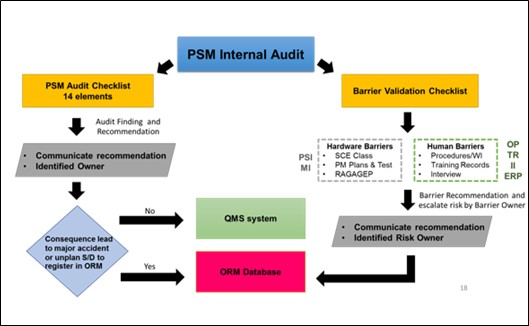
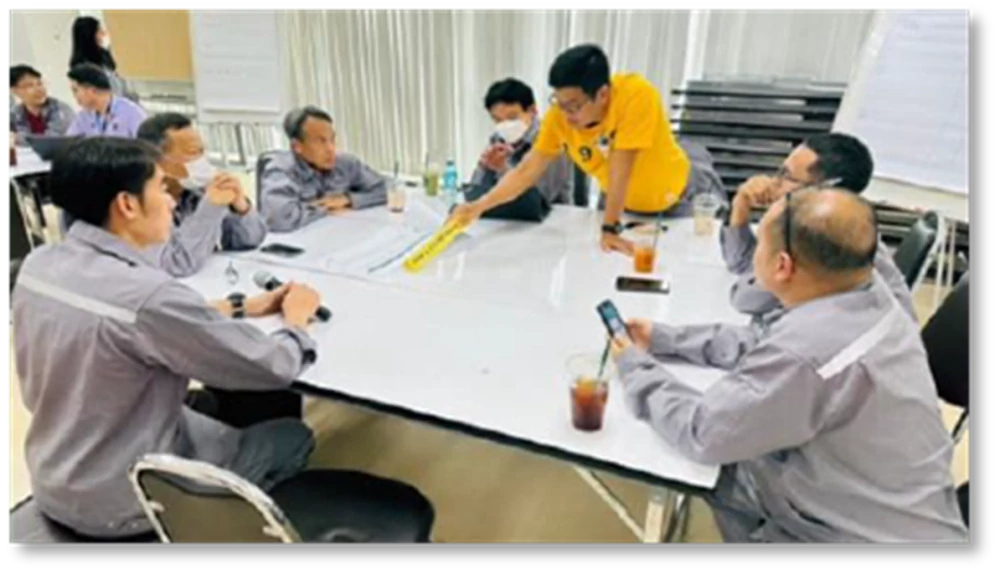
Enhancing Plant PSM Committee Performance
GC has worked to enhance Process Safety Management (PSM) by reviewing the Readiness of Plant PSM Committee in terms of their governance process and capability to ensure that proper and robust governance is implemented in accordance with specified standards as well as to inspire felt leadership in order to drive the safety culture.
In addition to the aforementioned process safety operations, GC also implements an internal audit system that covers occupation health, safety and environmental issues, namely Daily SHE Inspection, whereby the safety inspector verifies that onsite communications are carried out in line with the measures established in the Job Safety and Environmental Analysis (JSEA). This includes auditing the performance and readiness of supervisors, equipments, car conditions and transportation of objects within the operating area, and after-the-job cleanup as well as infectious disease control, prevention and control measures.Then, the safety inspector establishes a Daily SHE Inspection Report.
GC is intent on continually upgrading safety standards in our operations, monitoring the progress, and evaluating the results from relevant function to minimize accident rate in the production process as much as possible.
More information on other related highlight projects is available in GC Integrated Sustainability Report 2024, such as
- Enhancing Plant PSM Committee Performance: Reviewing the readiness of the Process Safety Management Committee to upgrade process safety management.
- Operation Risk Management Risk Treatment to Prevent LOPC: Monitoring and implementation in Operational Risk Management (ORM) to enhance risk management efficiency.
- Align Field Risk Assessment (FRA) Good Practices: The adopting of digital technology and best practices to identify and manage production-related risks in order to enhance operational efficiency.
Process Safety Event Tier 1 (Case)
Target
Process Safety Event Tier 1
Performance | Target | |||||
---|---|---|---|---|---|---|
2021 | 2022 | 2023 | 2024 | 2024 | 2027 | |
Process Safety Event Tier 1 (Case) | 0 | 2 | 1 | 0 | 0 | 0 |