ความปลอดภัยของกระบวนการผลิต
ความปลอดภัยของกระบวนการผลิต (Process Safety Management)
GRI 403-2 (2018), 403-4 (2018), 403-7 (2018)
บริษัทฯ ดำเนินงานด้านการจัดการความปลอดภัยในกระบวนการผลิต (Process Safety) โดยถือเป็นส่วนหนึ่งของระบบการบริหารจัดการที่เป็นเลิศของบริษัทฯ (GC Management System: GCMS) และจัดทำการประเมินความเสี่ยงด้วยวิธี Hazard and Operability Study หรือ HAZOP รวมถึงกระบวนการทำ Bow Tie Validation เพื่อกำหนดแผนการบริหารจัดการป้องกันและควบคุมความเสี่ยง ครอบคลุมตั้งแต่ขั้นตอนการออกแบบกระบวนการดำเนินงาน ขั้นตอนบำรุงรักษา และการทวนสอบมาตรฐานเป็นประจำทุกปี ทั้งในภาวะปกติและภาวะฉุกเฉินให้เหมาะสม ตลอดจนมีการทบทวนและปรับปรุงแผนฉุกเฉินให้ทันสมัยอยู่เสมอ เพื่อรักษามาตรฐานการปฏิบัติงานให้สามารถดำเนินการผลิตได้อย่างปลอดภัยและมีประสิทธิภาพ
ระบบการบริหารจัดการปฏิบัติการที่เป็นเลิศ
การบริหารจัดการป้องกันและควบคุมความเสี่ยงในกระบวนการผลิต GRI 403-2 (2018)
บริษัทฯ ประเมินความเสี่ยงในกระบวนการผลิตด้วยวิธี Hazard and Operability Study หรือ HAZOP ซึ่งเป็นการพิจารณาความอันตรายที่มีโอกาสเกิดขึ้นในกระบวนการผลิต เพื่อจัดลำดับความสำคัญ หาวิธีป้องกันความเสี่ยงและควบคุมความขัดข้องที่อาจเกิดขึ้นในระบบปฏิบัติการ รวมถึงจัดทำแผนการลดผลกระทบที่รุนแรงจากอุบัติการณ์ที่อาจเกิดขึ้น โดยบริษัทฯ จะประเมินความเสี่ยงในกระบวนการผลิตเพื่อสอบทานประสิทธิภาพของระบบความปลอดภัยเดิม และมีการติดตั้งอุปกรณ์เพิ่มเติม หรือมีการเปลี่ยนแปลงในกระบวนการผลิต ทั้งนี้กระบวนการทั้งหมดจะอยู่ภายใต้ความรับผิดและกำกับดูแลของ Technical Safety and PSM team เพื่อให้มั่นใจได้ว่าตลอดกระบวนการผลิตจะดำเนินการได้อย่างมีประสิทธิภาพ
GC HAZOP Study Process
ผลจากการประเมินความเสี่ยงและความอันตรายด้านอาชีวอนามัยและความปลอดภัยในการปฏิบัติงาน ในปี 2567 พบว่า ประเด็นความเสี่ยงที่สำคัญ ได้แก่ 1) Safety Risk (Process Safety Event): การรั่วไหลของสารเคมีอันตราย มีความเสี่ยงต่อความปลอดภัยในการปฏิบัติงาน และเกิด อุบัติเหตุร้ายแรงส่งผลให้บาดเจ็บ หรือเสียชีวิต และ 2) Safety Risk (Personal): ความเสี่ยงในการเกิดอุบัติเหตุ จากกิจกรรมการเดินเครื่องโรงงาน การบำรุงรักษา โครงการก่อสร้าง รวมทั้งกิจกรรมสนับสนุนอื่นๆ ซึ่งอาจนำไปสู่การเกิดอุบัติเหตุ ส่งผลกระทบต่อการบาดเจ็บหรือเสียชีวิต จากการทำงาน
นอกจากนี้ บริษัทฯ ยังดำเนินการจัดตั้ง Operational Area Core Team (OACT) และ Process Safety Management Taskforce (PSMT) ประจำแต่ละหน่วยผลิต เพื่อผลักดันให้เกิดการบริหารความปลอดภัยในกระบวนการผลิตอย่างทั่วถึงและเหมาะสมกับแต่ละพื้นที่ ซึ่งเป็นการสนับสนุนความมุ่งมั่นของบริษัทฯ ในการเป็นผู้นำของอุตสาหกรรมเคมีภัณฑ์ที่มีการดำเนินงานด้านอาชีวอนามัยและความปลอดภัยเทียบเท่ากับมาตรฐานสากล และบริษัทฯ ยังจัดทำมาตรการบริหารเสถียรภาพและสมรรถนะของเครื่องจักร (Reliability & Integrity) ของทุกโรงงาน และจัดตั้งทีมงานปรับปรุงเสถียรภาพของเครื่องจักร (Reliability Improvement Team: RIT) ทั้งนี้ เครื่องจักรในทุกโรงงานของบริษัทฯ จะต้องได้รับการตรวจประเมินประสิทธิผลการทำงานจากผู้เชี่ยวชาญจากภายใน ผ่านโปรแกรม Asset Integrity Assessment (AIA) เพื่อวิเคราะห์และกำหนดแผนปรับปรุงเสถียรภาพของเครื่องจักรที่ครอบคลุมทุกปัจจัยที่อาจทำให้เกิดอุบัติการณ์ ตลอดจนลดอัตราการหยุดการผลิตฉุกเฉิน (Unplanned Shutdown)
โครงการความปลอดภัยของกระบวนการผลิต GRI 403-2 (2018), 403-4 (2018)
บริษัทฯ ยกระดับมาตรฐานความปลอดภัยในกระบวนการผลิตอย่างต่อเนื่อง โดยประยุกต์ใช้เทคโนโลยีในการทำงาน พัฒนาและยกระดับโครงการนำร่องต่าง ๆ ที่ประสบความสำเร็จให้มีความครบถ้วนสมบูรณ์ โดยบริษัทฯ ได้จัดทำโครงการด้านความปลอดภัยในกระบวนการผลิตหลายโครงการ อาทิ โครงการยกระดับการดำเนินงานคณะกรรมการความปลอดภัยในกระบวนการผลิตของโรงงาน (Enhancing Plant PSM Committee Performance) โครงการยกระดับติดตามมาตรการจัดการความเสี่ยงในกระบวนการ ORM (Operation Risk Management Risk Treatment to Prevent LOPC) โครงการนำ Good Practice มาแลกเปลี่ยนเรียนรู้และยกระดับกระบวนการสร้าง File Risk Assessment (FRA)
ทั้งนี้เพื่อให้กระบวนการผลิตดำเนินการควบคู่ไปกับการรักษาความปลอดภัยที่เป็นไปตามมาตรฐานและข้อกำหนดทางกฎหมาย
โครงการ Smart Process Safety Event (PSE)
บริษัทฯ พัฒนาระบบดิจิทัลเพื่อสนับสนุนการจัดการ Integrity Operating Window (IOW) ให้มีประสิทธิภาพและประสิทธิผลสูงสุด ซึ่งระบบดิจิทัลนี้สามารถติดตาม Process Safety Near Miss (PSE Tier3b) เพื่อนำไปเฝ้าระวัง และคาดการณ์ถึงความเป็นไปได้ที่อุบัติเหตุจะเกิดขึ้น ตลอดจนจัดทำมาตรการรองรับความเสี่ยงอย่างเหมาะสม ซึ่งช่วยให้บริษัทฯ สามารถหลีกเลี่ยงความเสียหายของอุปกรณ์ หรือการหยุดชะงักในกระบวนการผลิต นอกจากนี้ ระบบดังกล่าวยังสามารถนำมาประยุกต์ใช้ในการประเมินอายุของอุปกรณ์ และการวางแผนการตรวจสอบ (Inspection) ได้อีกด้วย
โครงการนำ Good Practice มาแลกเปลี่ยนเรียนรู้ และยกระดับกระบวนการสร้าง Align Field Risk Assessment (FRA)
บริษัทฯ ได้ร่วมมือกับผู้เชี่ยวชาญจากบริษัท DuPont จัดทำโครงการ Field Risk Assessment เพื่อเสริมสร้างความรู้และความสามารถของพนักงานในการสังเกตและตระหนักถึงอันตรายและผลกระทบที่อาจจะเกิดขึ้นจากการเบี่ยงเบนจากมาตรฐานหรือขั้นตอนการทำงานที่กำหนด ซึ่งช่วยเพิ่มศักยภาพของระบบป้องกันและควบคุมอุบัติเหตุร้ายแรง (Barrier of Protection) และลดความเสี่ยงของการเกิดอุบัติเหตุจากกระบวนการผลิต โดยมุ่งเน้นทั้ง 3 ด้าน ได้แก่ ด้านบุคคล (Personnel) ด้านเครื่องมือ อุปกรณ์หรือสิ่งปลูกสร้าง (Facilities) และด้านเทคโนโลยี (Technology)
ในปี 2567 บริษัทฯ ยกระดับการจัดการความเสี่ยงด้านความปลอดภัยในพื้นที่ปฏิบัติงาน โดยนำแนวปฏิบัติที่ดีที่สุด (Best Practice) มาประยุกต์ใช้ และพัฒนาพนักงานระดับปฏิบัติการให้มีทักษะการเป็น Risk Sensor ผ่านการใช้งานฐานข้อมูล Field Risk Assessment Library (FRA Library) เพื่อเพิ่มประสิทธิภาพการป้องกันความเสี่ยงในการทำงาน โดยในปีนี้ พบว่าพนักงานระดับปฏิบัติการสามารถระบุความเสี่ยง และตรวจสอบ FRA sub-elements ได้ถึงร้อยละ 76
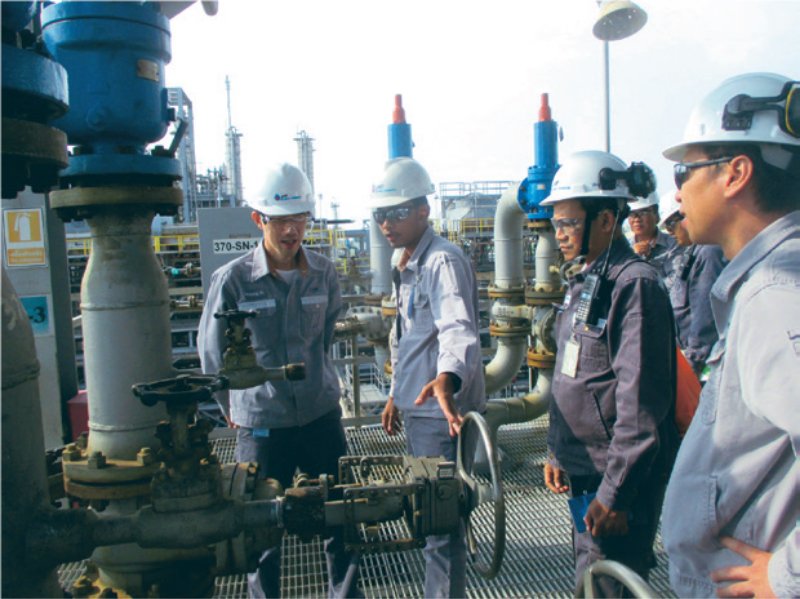
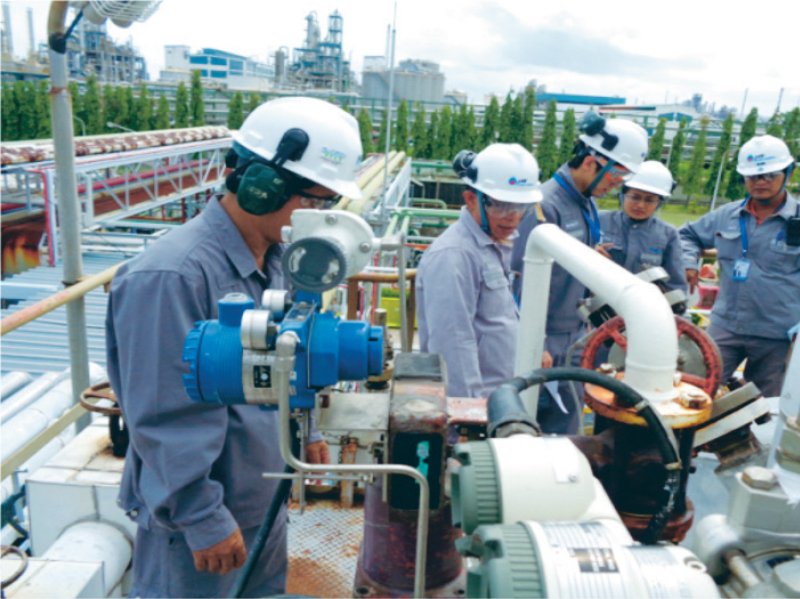
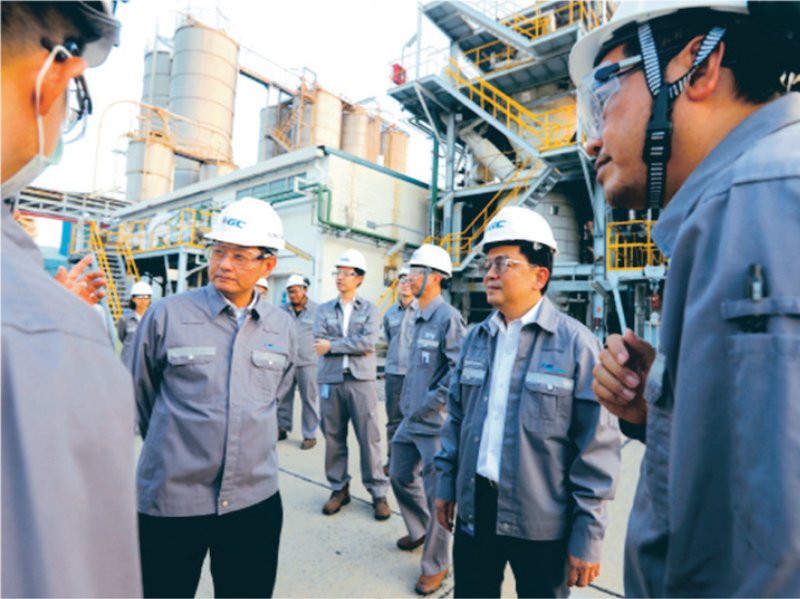
โครงการเสริมความแข็งแรง Bow Tie Barrier Validation
บริษัทฯ ได้นำการวิเคราะห์ความเสี่ยงแบบ Bowtie Analysis มาประยุกต์ใช้ เพื่อประเมินอันตรายหรืออุบัติเหตุที่อาจเกิดขึ้น รวมถึงผลกระทบจากเหตุการณ์ดังกล่าวที่อาจจะนำไปสู่ อุบัติการณ์ร้ายแรง (Major Accident Event: MAE) โดยได้ยกระดับการตรวจประเมินประสิทธิผลของการดำเนินการในแต่ละ Bowtie ด้วยการนำข้อมูลดังกล่าวมาตรวจสอบความถูกต้องครบถ้วนสมบูรณ์ โดยผสานเข้ากับการตรวจประเมินภายใน (Internal Audit) สำหรับการบริหารจัดการความปลอดภัยในกระบวนการผลิตรายปี ตามข้อบังคับของการนิคมอุตสาหกรรมแห่งประเทศไทย (กนอ.) เพื่อให้มั่นใจว่ามาตรการต่างๆ ที่กำหนดจะมีความพร้อมเพื่อป้องกันการเกิดอุบัติเหตุทางกระบวนการผลิต
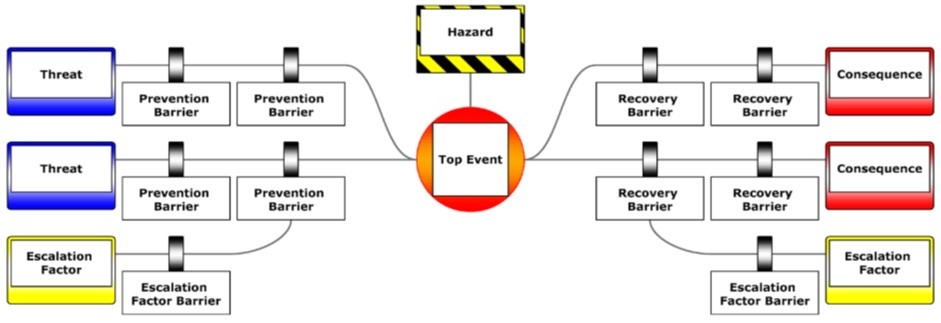
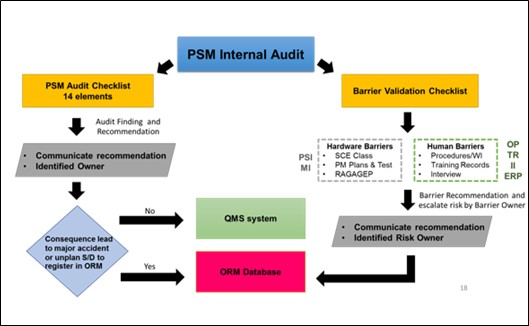
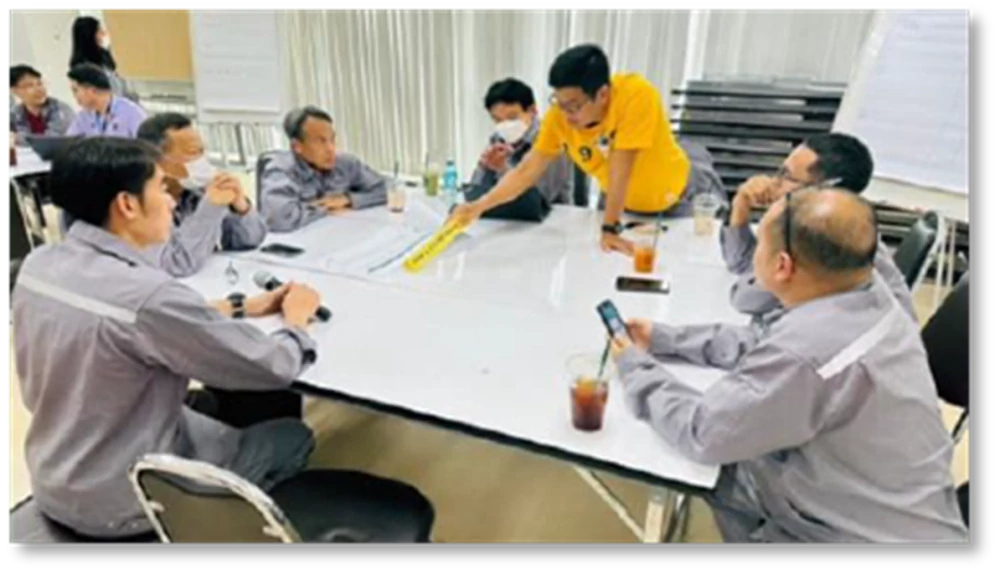
โครงการยกระดับการดำเนินงานคณะกรรมการความปลอดภัยในกระบวนการผลิตของโรงงาน (Enhancing Plant PSM Committee Performance
บริษัทยกระดับเรื่อง Process Safety Management (PSM) โดยการทบทวน Readiness of Plant PSM Committee ทั้งทางด้านการกำกับดูแล (Governance Process) และ ด้าน Capability ของคณะกรรมการ Plant PSM Committee ต่อเนื่อง เพื่อให้มั่นใจว่าได้มีการกำกับดูแลอย่างถูกต้อง เข้มแข็งตามมาตรฐานที่กำหนด รวมทั้งเป็นการกระตุ้น Felt Leadership เพื่อขับเคลื่อน Safety Culture
นอกเหนือจากการดำเนินงานด้านความปลอดภัยในกระบวนการผลิตที่กล่าวมาข้างต้น บริษัทฯ ยังมีระบบการตรวจสอบภายในที่ครอบคลุมด้านอาชีวอนามัยและความปลอดภัย และด้านสิ่งแวดล้อม ได้แก่ Daily SHE Inspection ซึ่งผู้ตรวจสอบด้านความปลอดภัย (Safety Inspector) จะตรวจสอบการสื่อสารหน้างานที่สอดคล้องกับมาตรการที่กำหนดไว้ใน Job Safety and Environmental Analysis หรือ JSEA ซึ่งเป็นการตรวจสอบการทำงานและความพร้อมของหัวหน้างาน การตรวจสอบอุปกรณ์ สภาพรถ และการขนย้ายสิ่งของในพื้นที่ปฏิบัติงาน และการจัดเก็บพื้นที่เมื่อปฏิบัติงานแล้วเสร็จ รวมถึงมาตรการป้องกันและควบคุมโรคติดต่อ โดยผู้ตรวจสอบด้านความปลอดภัยจะจัดทำรายงานสรุปผลการตรวจสอบ (Daily SHE Inspection Report) เพื่อรายงานต่อผู้เกี่ยวข้องต่อไป
ทั้งนี้ บริษัทฯ มีความตั้งใจที่จะพัฒนามาตรฐานความปลอดภัยในกระบวนการผลิต ตลอดจนติดตามและประเมินผลการดำเนินการของหน่วยงานที่เกี่ยวข้องอย่างต่อเนื่อง เพื่อให้อัตราการเกิดอุบัติเหตุในกระบวนการผลิต ซึ่งเป็นเป้าหมายการบริหารงานด้านความปลอดภัยของบริษัทฯ มีแนวโน้มลดลงให้มากที่สุดอย่างเต็มความสามารถ
สามารถดูรายละเอียดโครงการโดดเด่นอื่น ๆ ที่เกี่ยวข้อง เพิ่มเติมได้ที่ GC Integrated Sustainability Report 2567 อาทิ
- โครงการยกระดับการดำเนินงานคณะกรรมการความปลอดภัยในกระบวนการผลิตของโรงงาน (Enhancing Plant PSM Committee Performance) การทบทวนความพร้อมเพรียงของคณะกรรมการด้านการบริหารจัดการความปลอดภัยในกระบวนการผลิต
- โครงการยกระดับติดตามมาตการจัดการความเสี่ยงในกระบวนการ ORM (Operation Risk Management Risk Treatment to Prevent LOPC) การติดตามมาตรการจัดการความเสี่ยงด้านปฏิบัติการ (Operational Risk Management: ORM) เพื่อเพิ่มประสิทธิภาพในการบริหารจัดการความเสี่ยง
- โครงการนำ Good Practice มาแลกเปลี่ยนเรียนรู้ และยกระดับกระบวนการสร้าง Field Risk Assessment การประยุกต์ใช้เทคโนโลยีดิจิทัลและแนวปฏิบัติที่ดีที่สุด (Best Practice) ในการค้นหาและจัดการความเสี่ยงด้านการผลิต เพื่อเพิ่มประสิทธิภาพการดำเนินงาน
ผลการดำเนินงานด้านความปลอดภัยในกระบวนการผลิต (Process Safety Event Tier 1)
จำนวนกรณีที่เกิด
เป้าหมาย
ผลการการดำเนินงานด้านความปลอดภัยในกระบวนการผลิด (Process Safety Event Tier 1)
ผลการประเมิน | เป้าหมาย | |||||
---|---|---|---|---|---|---|
2564 | 2565 | 2566 | 2567 | 2567 | 2570 | |
จำนวนกรณีที่เกิด | 0 | 2 | 1 | 0 | 0 | 0 |