โครงการลดการปล่อยมลพิษทางอากาศ
บริษัทฯ ดำเนินโครงการที่เกี่ยวข้องกับประสิทธิภาพการควบคุมมลพิษทางอากาศ ทั้งภายในพื้นที่ปฏิบัติการและบริเวณโดยรอบของพื้นที่บริษัทฯ ให้อยู่ในเกณฑ์มาตรฐานตามกฎหมาย ระเบียบข้อบังคับ และหลักมาตรฐานสากล นอกจากนี้ ยังเป็นตัวแทนกลุ่มอุตสาหกรรมปิโตรเคมีร่วมกับภาครัฐในการกำหนดแนวทางการจัดการมลพิษทางอากาศ โดยประยุกต์ใช้นวัตกรรมที่ทันสมัยเพื่อให้เกิดประสิทธิผลสูงสุด ผ่านคณะทำงานซึ่งเป็นเครือข่ายที่เข้มแข็งในการจัดการสิ่งแวดล้อม
บริษัทฯ ควบคุมการปล่อยก๊าซประเภทออกไซด์ของไนโตรเจน (NOx) และก๊าซออกไซด์ของซัลเฟอร์ (SOx) จากกระบวนการผลิตตามมาตรฐานที่กำหนดในรายงานการประเมินผลกระทบสิ่งแวดล้อม (Environmental Impact Assessment: EIA) และกฎหมายไทยอย่างสม่ำเสมอ โดยบริษัทฯ จัดทำโครงการเพื่อตรวจ ติดตาม และเฝ้าระวังผลการปล่อย NOx และ SOx อาทิ
- ใช้ระบบการตรวจวัดมลพิษทางอากาศแบบอัตโนมัติอย่างต่อเนื่อง (Continuous Emissions Monitoring System: CEMS) และติดตามคุณภาพอากาศโดยห้องปฏิบัติการภายนอกที่ได้รับการขึ้นทะเบียนเป็นระยะ
- ปรับปรุงระบบกังหันโดยใช้ก๊าซ (Gas Turbines) และระบบการเผาไหม้ที่ลดการก่อตัวของก๊าซ NOx (Ultra Low NOx Burner) เพื่อลดมลพิษจาก NOx ที่ปล่อยออกจากแหล่งกำเนิด
- จัดทำนโยบายในการเลือกใช้วัตถุดิบและเชื้อเพลิง ที่ส่งผลกระทบต่อสุขภาพและสิ่งแวดล้อมให้น้อยที่สุด
- ใช้เชื้อเพลิง และวัตถุดิบตั้งต้นที่มีปริมาณซัลเฟอร์ต่ำ เพื่อลดการปล่อย SOx จากการเผาไหม้
- ลดปริมาณการใช้น้ำมันเชื้อเพลิง เพื่อลดปริมาณการปล่อย SOx
ในปี 2567 มีโครงการที่โดดเด่นด้านการปรับปรุงประสิทธิภาพการปล่อยมลพิษทางอากาศ ดังนี้
มาตรการควบคุมสารเบนซีน (Benzene) และ 1,3-บิวทาไดอีน (1,3-Butadiene)
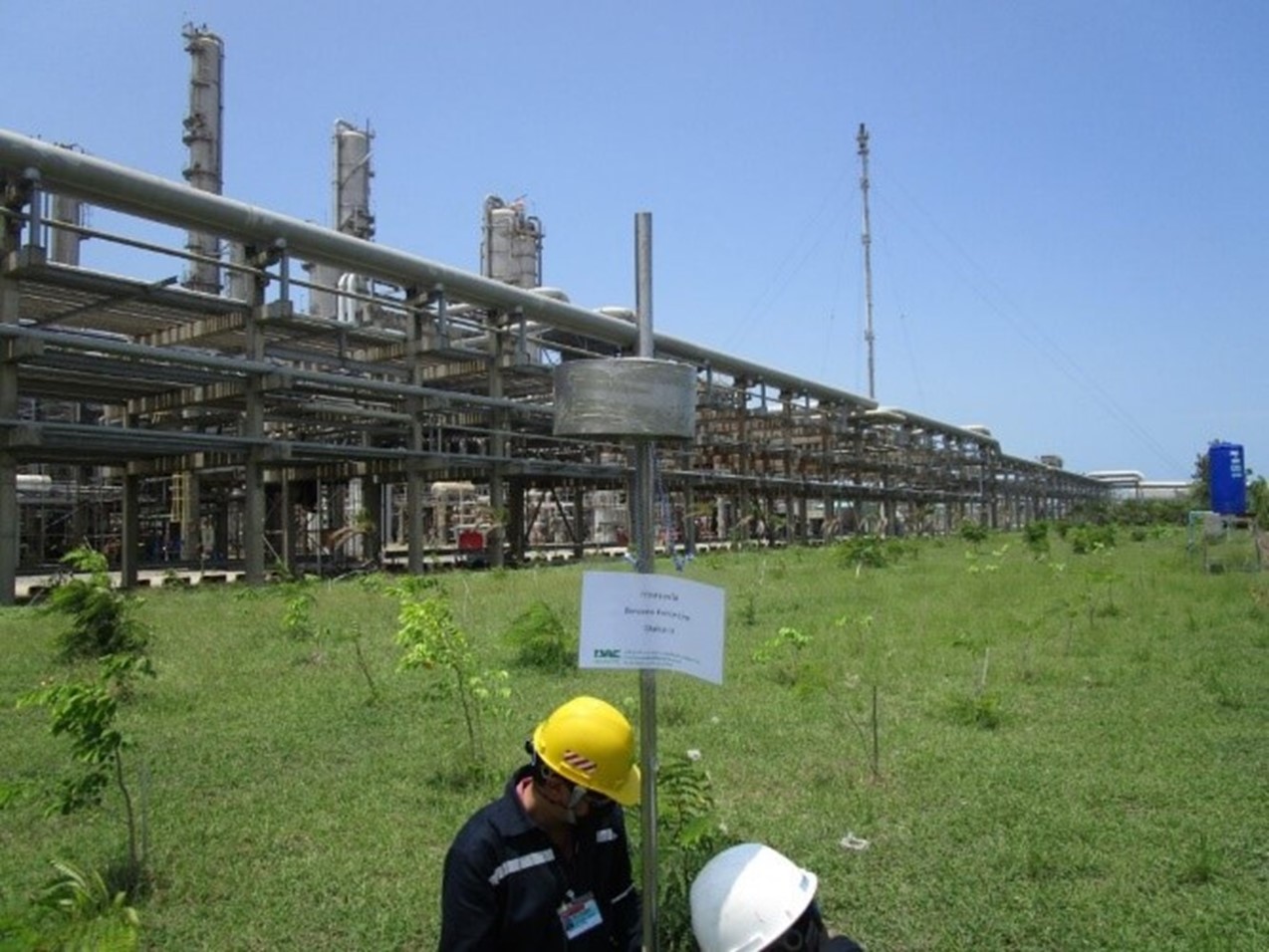
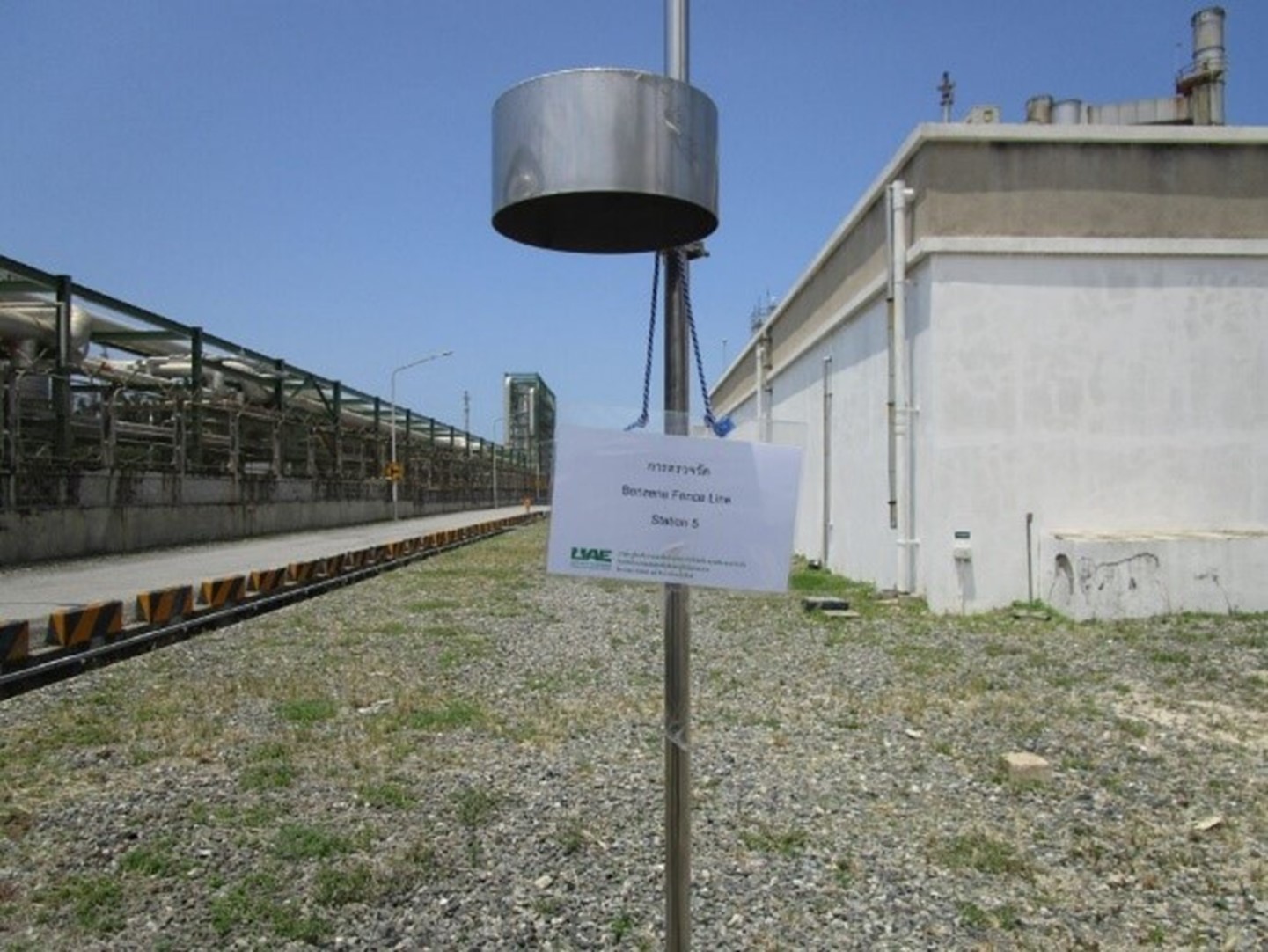
บริษัทฯ เข้าร่วมโครงการการปฏิบัติตามแนวการปฏิบัติที่ดี (Code of Practice) ของกรมโรงงานอุตสาหกรรมอย่างเคร่งครัด ซึ่งเป็นความร่วมมือระหว่างการนิคมอุตสาหกรรมแห่งประเทศไทยและกลุ่มอุตสาหกรรมปิโตรเคมีในพื้นที่มาบตาพุดคอมเพล็กซ์ ประกอบด้วย พื้นที่ 5 นิคมฯ และ 1 ท่าเรือ
ทั้งนี้ บริษัทฯ ดำเนินการเก็บตัวอย่าง สารเบนซีน และ 1,3-บิวทาไดอีน ริมรั้วโรงงาน ร่วมกับการนิคมอุตสาหกรรมมาบตาพุด เพื่อเป็นแนวทางการกำหนดค่ามาตรฐานในการเฝ้าระวังติดตามสารเบนซีน และ 1,3-บิวทาไดอีนริมรั้วโรงงาน โดยกำหนดจุดตรวจวัดให้ครอบคลุมพื้นที่ริมรั้วโรงงาน และทำการเก็บตัวอย่างดังกล่าว ตามมาตรฐาน USEPA Method 325A และ 325B เพื่อให้ศึกษาแนวโน้มคุณภาพอากาศของพื้นที่ โดยบริษัทฯ มีการบริหารจัดการสารอินทรีย์ระเหยง่าย (VOCs) โดยยึดหลักกลไกการปฏิบัติที่ดี (Code of Practice) อันนำไปสู่การกำหนดเป็นค่ามาตรฐานที่เหมาะสมต่อไป
โครงการพัฒนาระบบเฝ้าระวังการระบายมลพิษแบบคาดคะเน (Predictive Emission Monitoring System: PEMs)
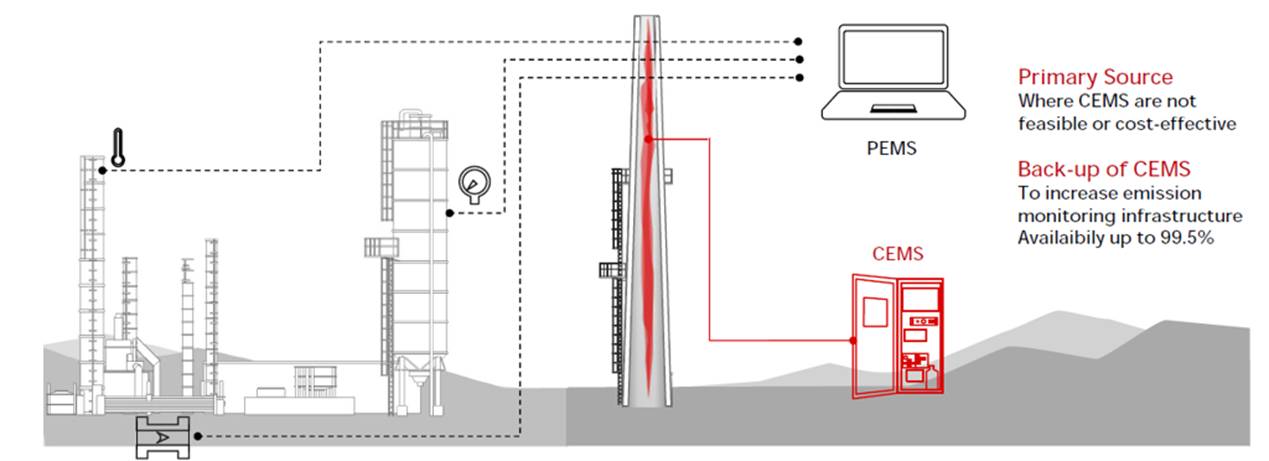
บริษัทฯ เข้าร่วมคณะทำงานคลัสเตอร์ปิโตรเคมี สภาอุตสาหกรรมแห่งประเทศไทย เพื่อศึกษาทางเลือกในการเฝ้าระวังการระบายมลพิษด้วยการคำนวณตามหลักการวิศวกรรมเคมีโดยไม่ต้องเจาะปล่องระบายก๊าซที่เกิดจากการเผาไหม้เพื่อติดตั้งเครื่องมือวัดอัตราการไหลของก๊าซไอเสีย (Flue gas) รวมถึงการค่าพารามิเตอร์อื่น ๆ เช่น ก๊าซซัลเฟอร์ออกไซด์ (SOx) ก๊าซไนโตรเจนออกไซด์ (NOx) และก๊าซคาร์บอนมอนอกไซด์ (CO) เป็นต้น โดยศึกษาระบบเฝ้าระวังการระบายมลพิษแบบคาดคะเน (Predictive Emission Monitoring System :PEMS) เพื่อประเมินการปล่อยมลพิษจากโรงงานอุตสาหกรรม โดยใช้แบบจำลองทางคณิตศาสตร์ในการทำนายการปล่อยมลพิษ ผ่านการรวบรวมข้อมูลจากเซ็นเซอร์ที่ติดตั้งในกระบวนการผลิต อาทิ อุณหภูมิ ความดัน และอัตราการไหลของเชื้อเพลิง แทนการวัดค่ามลพิษโดยตรง ส่งผลให้สามารถตรวจวัดได้อย่างต่อเนื่อง ประหยัดค่าใช้จ่าย และช่วยให้โรงงานปรับปรุงกระบวนการผลิตได้อย่างมีประสิทธิภาพ