Hazardous Substance Management and Performance
With a commitment to reduce, limit and terminate the use of hazardous chemicals, which may harm the environment and the health of employees and consumers, GC has reviewed national and international laws, regulations, and standards related to the termination or control of chemical use, e.g. the List of Hazardous Substances according to the Department of Industrial Works, the Montreal Protocol on Substances that Deplete the Ozone Layer, the Registration, Evaluation, Authorization and Restriction of Chemicals (REACH), and the Restriction of Hazardous Substances (RoHs), etc. The objective of such action is to regulate the use of chemicals throughout the life cycle of product.
In 2024, GC established the target to develop environmentally friendly products and limit environmentally harmful products in our portfolio (as defined in the Annex XVII of the Registration, Evaluation, Authorisation and Restriction of Chemicals (REACH) regulation) where revenue from these products must not exceed 3% of the Company’s total product revenue. As a result, GC was able to successfully limit revenue from environmentally harmful products to 2% of the Company’s total product revenue.
Additionally, GC has a commitment to phasing out PFAS from Metallocene Linear Low-Density Polyethylene (mLLDPE) products for the Flexible Packaging group by 2025. The increasing global concern over the potential environmental and health hazards posed by PFAS substances has led several nations, including the United States and the European Union, to contemplate regulatory measures. This deliberation encompasses the assessment and potential imposition of restrictions aimed at prohibiting the utilization of PFAS substances as ingredients in products. For example, US EPA published a final rule under the Toxic Substances Control Act (TSCA) that requires all manufacturers (including importers) of PFAS and PFAS-containing articles to report information to EPA on PFAS uses, disposal, and hazards. GC has started to researching and conducting laboratory on using alternative materials that is safe for environment and not containing the PFAS in 2023. Additionally, By the end of 2024, GC could manufacture PFAS free product from mLLDPE for the Flexible Packaging group for commercial purposes. In 2025, the Company continued its operations as planned and successfully launched its products to the market, receiving positive feedback from customers. There are also plans to expand to other products of the Company.
GC is committed to substituting hazardous substances and to phasing out hazardous substances. The company transparently monitors and reports on the progress towards meeting these targets on a regular basis and seeking collaboration with industry associations to identify viable substitutes for hazardous substances. Furthermore, the company allocates dedicated resources and budgets for research and development (R&D) to achieve its goals of substituting and phasing out hazardous substances in products. The Company allocated a budget of 90,000 baht in 2024 and an additional 1 million baht in 2025 for the research and development of PFAS-free products.
The collaboration with TIPMSE to drive the Design for Recycling Guideline for sustainable packaging

GC has participated in the development of the “Packaging Design for Recycling Guideline” which takes into consideration the impacts on the supply chain and stakeholders across all stages of the packaging life cycle. This initiative is carried out in collaboration with the Thailand Institute of Packaging and Recycling Management for Sustainable Environment (TIPMSE) under the Federation of Thai Industries (FTI), along with relevant public and private sector organizations. The objective is to promote packaging design that supports recyclability, with a focus on eliminating the use of Polyvinyl Chloride (PVC) labels on Polyethylene Terephthalate (PET) bottles, as PVC is considered a hazardous substance that can significantly degrade the quality of recycled PET products.
GC has also prepared the Product Safety and Toxicity Disclosure, and has communicated relevant information to employees and suppliers, in order to ensure that the chemicals used in the production process comply with related regulations and laws. GC has provided its customers with the instruction on the safe management of its products through the product labelling in accordance with United Nation’s Globally Harmonized System of Classification and Labelling of Chemicals (GHS) standard. This includes product usage, storage transportation, disposal, etc.
Safety Data Sheet (SDS)
69% of GC’s products have been subjected to chemical group classification with labeling and safety data sheets on health and environmental hazards according to the Globally Harmonised System for Classification and Labeling of Chemicals (GHS). GC develops the Safety Data Sheet (SDS) in an alignment with Globally Harmonised System for Classification and labeling of Chemicals (GHS) to communicate safety information of hazardous substances with internal and external stakeholders, including operators, customers, community, supplier, industrial estate and government. GC also incorporates information in regard to medical treatment and long-term follow-up for the individuals who take risks associated with hazardous substance in products, into the SDS. The SDS is publicly available on website (one page format) in both Thai and English versions, as well as launched in a form of mobile application for the contractor.
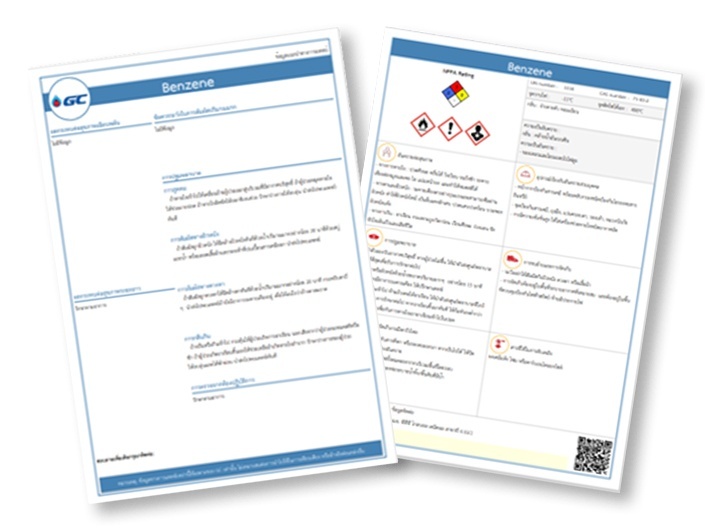
In addition, the company are aware of the environmental impacts from the use of the hazardous substance. In this regard, GC continues to research and develop products to reduce the use of hazardous chemicals or transform into safer chemicals, as we as prioritize and schedule operations to minimize environmental and human health impacts.
Risk Assessment of Hazardous Substances in Products
GC conducts a risk assessment of hazardous substances in products throughout “Cradle-to-Gate” boundary, including raw material acquisition, manufacturing process, and transportation. GC performs the Risk Assessment of Hazardous Substances in Products in the value chain, focusing on two aspects, namely Human Health Risk Assessment of Hazardous Substances in Products, and Environmental Risk Assessment of Hazardous Substances in Products. In terms of the product risk assessment, GC refers to the data from relevant toxicological study and eco-toxicological summary performed by internal and external laboratory research, reference disclosed in national and international levels, and practical data recorded in the using terms (i.e. physicochemical properties and work environment conditions).
Human Health Risk Assessment of Hazardous Substances in Products
In the compliance with Notification of the Ministry of Industry Issue No. 4439 (2555) Issued under the Industrial Product Standards Act 1968 Subject: Defining industrial product standards Health risk assessment for chemical workers in industrial plants, GC has developed software and guideline, product risk evaluation criteria, hazard risk assessment diagram for human health and environment.
The human health risk assessment procedures involve in five steps, including 1) Hazard identification, 2) Does-response assessment, 3) Exposure assessment, 5) Risk control.
Process of Human Health Risk Assessment of Hazardous Substances in Products
Substances are categorized through the risk evaluation matrix that mainly considers two factors, such as hazard and frequency of exposure. The risk classification is specified in five levels, including level 0: Acceptable Risk, level 1: Low Risk, level 2: Moderate Risk, level 3: High Risk, and level 4: Very High Risk.
Criteria of Human Health Risk Assessment of Hazardous Substances in Products: Hazard Rating
Level | Hazard | Impact on human health |
---|---|---|
1 | No Hazard | No effect in human health |
2 | Low hazard | Small effect on human health. There are no such conditions, namely medical treatment, sick leave and cause of disability involved. |
3 | Medium Hazard | Slightly effect on human health. There are such conditions, namely medical treatment, sick leave and cause of disability involved. |
4 | High Hazard | Permanently effect on human health. There are consequences as such severe injury, incurable and long-term sickness conditions involved. |
5 | Very High Hazard | Fatality or disability. |
Criteria of Human Health Risk Assessment of Hazardous Substances in Products: Average Chemical Concentration throughout operation
Concentration level | Average Chemical Concentration throughout operation |
---|---|
1 | Below 10% of OEL-TWA |
2 | Below 50% of OEL-TWA |
3 | Below 75% of OEL-TWA |
4 | Between 75% - 100% of OEL-TWA |
5 | Exceed 100% of OEL-TWA |
Criteria of Human Health Risk Assessment of Hazardous Substances in Products: Frequency of Exposure
Level | Frequency | Frequency of Exposure | Shift Operation (12 hours.) |
---|---|---|---|
1 | Rarely | Expose once a year | Once a year |
2 | Infrequently | Expose 2-3 times a year | Once a month |
3 | Frequently | Expose 2-3 times a month | 1-2 hours per shift operation |
4 | Likely frequently | Continually Expose 2 – 4 hours per shift operation | 4-6 hours per shift operation |
5 | Regularly | Entirely expose throughout shift operation | 12 hours per shift operation |
Additionally, GC has also set controlling measures for the risk identified as per to the criteria matrix below.
Scoring | Risk Category | Risk level | Measures |
---|---|---|---|
1-3 | Acceptable | 0 | Risk shall be monitored regularly |
4-9 | Low | 1 | Risks shall be closely monitored and reassessed regularly |
10-16 | Moderate | 2 | Controlling measures shall be provided immediately |
17-20 | High | 3 | Controlling measures shall be provided immediately. Long-term controlling plans shall be conducted |
21-25 | Very high | 4 | Product shall be terminate immediately |
Human Health Risk Assessment of Hazardous Substances in Products
GC conducted Human Health Risk Assessment of Hazardous Substances in Products for total all products (40 groups of products) that may affect employee’ and operators’ health, covering job positions, such as Division Manager, Shift Manager/Day Manager, Field Operator and Contractor, covering all GC products (40 product groups) through HRA Software to maintain information up to date at all times. As a result, all products were addressed to low risks.
For those identified risks, GC has set controlling measures in place to ensure that our employees’ health and well-being and have proper understanding about preventive measures for the hazardous substances as follows;
- Wearing chemical protection mask
- Wearing safety goggle
- Wearing chemical protection gloves
- Wearing safety shoes
- Monitoring on workers’ health, and harmful areas for each job position
Apart from assessing the Human Health Risk of Hazardous Substances in Products that affect workers’ and users’ health, GC has also conducted the Environmental Risk Assessment of Hazardous Substances in Products in consistent with the criteria and regulations of the International Council of Chemicals Association (ICCA).
Environmental Risk Assessment of Hazardous Substances in Products
Process of environmental Risk Assessment of Hazardous Substances in Products
Reference: The GPS Risk Assessment Process, ICCA Guidance on Chemical Risk Assessment
GC refers to the several sources of information, namely Safety Data Sheet (SDS) that is publicly disclosed for stakeholders, toxicological studies from European Chemicals Agency (ECHA), and GHS Classification Databases according to UN GHS Category, in order to classify the hazards of hazardous substances, covering 100 percent of products. GC also uses REACH registration as references to screen out product risks. As a result, there were 69 percent of products under REACH registration, thus, these products were proceeded to prioritize in four priorities for risk assessment according to ICCA guidance. The result showed that 49 percent of total products were classified in Priority 4 Very Low Hazard/Exposure Potential and 21 percent of total products were classified in Priority 3: Low Hazard/Exposure Potential. In addition to the result, GC proceeded to use ECETOC TRA, a calculation tool to implement Hazard Characterization by considering several environmental factors, namely Microorganisms in STP, Freshwater aquatic, Freshwater sediment, Marine water, Marine sediment and Terrestrial compartment.
According to Risk Management Category (RMC) of ICCA, identified risks associated with 3 percent of total products were classified in Medium risk for environment. However, GC has controlling and monitoring measures to ensure that quality of entire environmental aspects are in line with standards and potential environmental impacts are controlled properly.
Preventive and Controlling Measures for the Environmental Impacts
GC values importance of preventive measures to avoid such environmental impacts. We designate preventive and controlling procedures throughout the implementation of project starting with designing phase, and thoroughly conduct feasibility of environmental impacts of each project through Environmental Impact Assessment Reporting (EIA). GC also strictly complies with the preventive and controlling measures as well as continually reports monitoring results to relevant government parties on a regular basis. More importantly, GC brings over practices of international standard ISO 14001 and environmental management systems and apply them as a foundation of our implementation process. Other best practices, such as Environmental, Health and Safety Guidelines by International Finance Corporation (IFC) (World Bank Group) and Internet of Things (IoT) are integrated in the measures. Examples of Preventive and controlling measures for the environmental impacts are as follows;
Environmental impacts | Preventive and controlling measures |
---|---|
Air Quality |
|
Water Quality |
|
Soil Quality |
|