Personal Safety Management
Personal Safety Management GRI 403-7 (2018) GRI 403-4 (2018)
Our comprehensive safety culture goes beyond implementing safety regulations. It includes constant awareness and integrating safety standards and measures into our company. GC set target for Personal Safety Management and regularly monitor results through clear indicators, such as TRIR (Total Recordable Injuries Rate) at 0.45 cases per one million man-hours, with a long-term target of less than 0.35 cases per one million man-hours by 2027, and LTIFR (Lost Time Injuries Frequency Rate) at 0.00 case per one million man-hours.
GC has also recorded and analyzed the historical and statistical data that are equivalent to global safety standard to enhance the safety culture for employee at all level. As a result, the company’s personal safety statistics are placed in the 1st Quartile according to the standard of International Association of Oil & Gas Producers (IOGP). In this regard, we analyze other safety data to develop the Life Saving Rules.
Life-Saving Rules
Always use safety harness when working at height
Always operate according to work permit
Assess energy isolation prior to working
Always operate according to working in confined space permit
Always operate according to first-time startup equipment standards.
GC has implemented the several personal safety projects, including Onsite Supervision with Permit to Work using e-PTW, e-JSEA and e-LOTO Early Detect Low-Performance Contractors, and Risk Management using Engineering Control.
Risk Management using Engineering Control GRI 403-7 (2018)
The assessment of operators’ safety risks as well as statistics on accidents and injuries have indicated that the majority injuries occur to their hands and fingers. Consequently, GC has initiated the Hand Injuries Awareness Program since 2017. This program focuses on raising employee awareness on accidents and collaborating with contractors to develop appropriate working tools to reduce the injury rate of employees and contractors. This year, GC has applied engineering control principles to improve protection from injuries by developing hand injury protective tools, such as wrenches with straps and slugging wrenches with spring handle. Moreover, GC has published a user manual for operators as a guideline to selecting the suitable tool for the job. GC also Classified tasks with high hand injury risk into 7 equipment groups, namely 1. Handle Lock and Slugging Wrench 2. Hydraulic Flange Spreader 3. Wage 4. Flange Alignment 5. Pipe Mover 6. Grating Lifter and 7. Automated High Pressure Water Jet.
Furthermore, GC has defined hand injury prevention as one of the assessment criteria for suppliers and contractors.
GC has also incorporated requirements relating to Special Tools as one of the criteria for evaluating suppliers and contractors, with special focus on activity groups that are the main causes of hand injuries. GC has obligated the use of 7 Special Tools according to the established equipment groups in all employment contracts, requiring suppliers and contractors to use risk and accident-reduction equipment recognized by GC upon performing tasks.
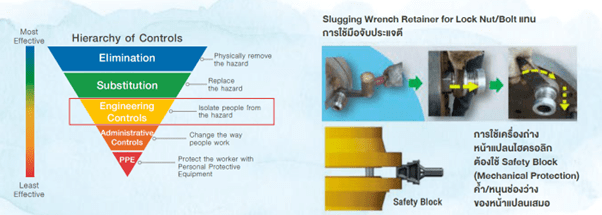
GC has strengthened the safety standards and reliability of operating sites by establishing additional occupational safety requirements in the Service Level Agreement and defined OHS criteria for contracts and procurement requirements. Suppliers are required to possess working permit and have safety management systems as well as safety measures for their personnel. Furthermore, GC has managed its supplier risk by verifying the qualifications of suppliers. GC has conducted assessment on the suppliers’ safety performance on an annual basis. The Supplier ESG Audit has also been implemented on suppliers in order to ensure that quality suppliers and contractors are sourced in line with to GC’s safety standards. Furthermore, GC has established the Occupational Health, Safety and Workplace Committee which consists of representatives from employees to oversee the company’s safety operations and organize monthly meetings to monitor performance progress.
In 2024, the TRIR was on a downward trend at 0.17 per 1 million man-hours, and the LTIFR was on a downward trend at 0 per 1 million man-hours as well.
GC commits to improving our safety operations and aims to demonstrate good safety leadership within the organization.
More information on other highlight projects is available in GC Integrated Sustainability Report 2024, such as
- Onsite Supervision with Permit to Work using e-PTW, e-JSEA and e-LOTO
- Early Detect Low-Performance Contractors
Total Recordable Injury Rate: TRIR (cases per 1 million man-hours)
Target
Year | Target | |||||
---|---|---|---|---|---|---|
2021 | 2022 | 2023 | 2024 | 2024 | 2027 | |
Employees (TRIR) | 0.48 | 0.46 | 0.06 | 0.33 | 0.45 | 0.35 |
Contractors (TRIR) | 1.00 | 0.59 | 0.77 | 0.38 | 0.45 | 0.35 |
Lost Time Injury Frequency Rate (LTIFR) (cases per 1 million man-hours)
Target
Year | Target | |||||
---|---|---|---|---|---|---|
2021 | 2022 | 2023 | 2024 | 2024 | 2027 | |
Employees (LTIFR) | 0.06 | 0.00 | 0.00 | 0.00 | 0.00 | 0.00 |
Contractors (LTIFR) | 0.32 | 0.09 | 0.24 | 0.00 | 0.00 | 0.00 |